Peak business seasons—like holiday rushes or harvest periods—can push logistics to the breaking point. Surging demand, tight carrier capacity, and delivery deadlines create a perfect storm for shippers. Streamlining your logistics is the key to staying ahead, ensuring your goods reach customers without delays or skyrocketing costs.
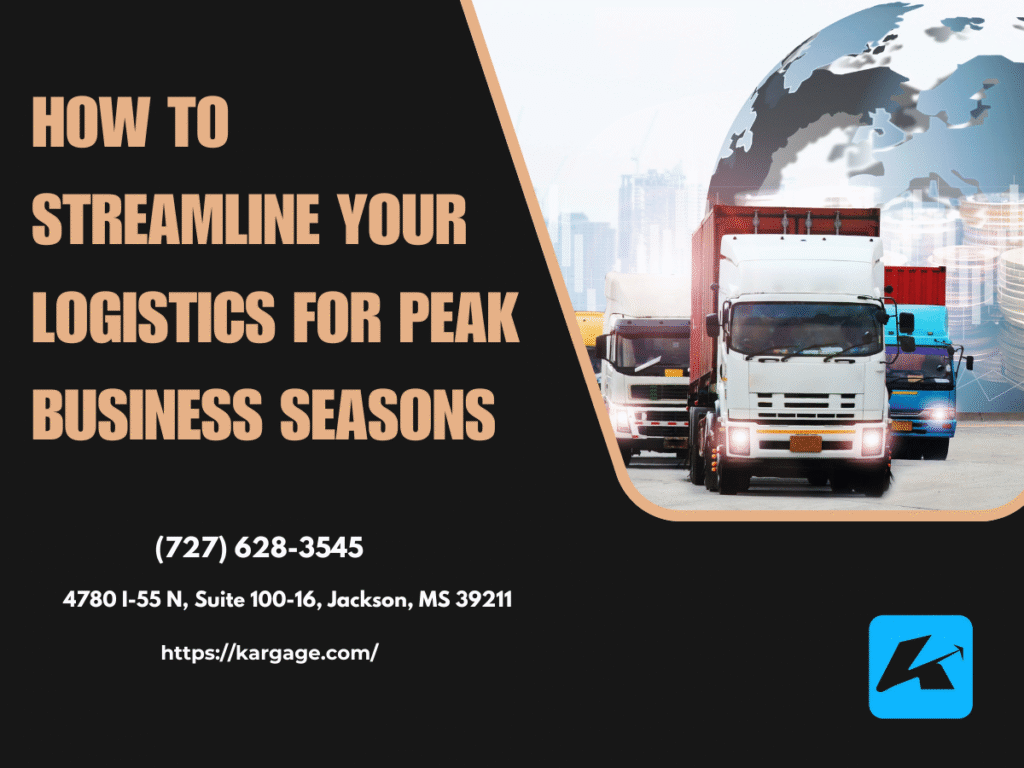
How do you keep your supply chain humming when the pressure’s on?
This guide shares five practical strategies to optimize your logistics for peak seasons and keep your business thriving.
1. Plan Early and Forecast Demand
Preparation is your best weapon against peak season chaos. Start by forecasting demand using historical sales data, market trends, and customer insights. For example, if you ship holiday gifts, analyze last year’s order spikes to predict inventory needs.
Map your supply chain—suppliers, carriers, and delivery points—and identify potential bottlenecks, like port delays or driver shortages. Book carriers and secure inventory months in advance to lock in capacity and rates.
Early planning prevents last-minute scrambles and premium costs.
Pro Tip: Use demand planning software or consult sales teams to refine forecasts. Start planning 3–6 months before your peak season kicks off.
2. Optimize Inventory Management
Overstocking ties up cash, while understocking loses sales. During peak seasons, smart inventory management keeps your logistics lean.
Implement just-in-time (JIT) inventory to reduce storage costs, but maintain a safety stock for unexpected surges. Use warehouse management systems (WMS) to track stock levels and prioritize high-demand items. For instance, a retailer might stage holiday inventory closer to key markets to speed up delivery.
Efficient inventory keeps your supply chain agile and responsive.
Action Step: Audit your inventory monthly before peak season. Adjust stock based on forecasts and place critical items in strategic locations.
3. Partner with Reliable Carriers and Brokers
Peak seasons strain carrier capacity, making reliable partners essential. Build relationships with carriers who can handle your volume and meet deadlines, whether for dry van, refrigerated, or expedited freight.
A freight broker can simplify this, connecting you to a network of vetted carriers. Kargage, based in Jackson, Mississippi, links shippers with over 25,000 carriers to secure capacity during crunch times.
Strong partnerships ensure your freight gets priority when trucks are scarce.
Quick Tip: Negotiate contracts with carriers early. Discuss peak season needs and secure commitments for extra trucks or priority slots.
4. Leverage Technology for Efficiency
Technology is a game-changer during peak seasons. Transportation Management Systems (TMS) optimize routes, consolidate loads, and track shipments in real time. Real-time visibility lets you reroute cargo around delays, like a congested port, or adjust schedules on the fly.
For example, GPS tracking can confirm a refrigerated load stays at 35°F, while predictive analytics flag potential disruptions. Digital platforms also streamline communication with carriers and customers, cutting errors.
Kargage uses tech to help clients stay ahead, ensuring smooth logistics even in peak chaos.
Best Practice: Invest in a TMS or tracking tool. Ensure your carriers provide real-time updates to keep you in control.
5. Communicate and Stay Flexible
Peak seasons are unpredictable—weather, labor strikes, or demand spikes can throw plans off. Clear communication and flexibility keep your logistics on track.
Share forecasts and schedules with carriers, suppliers, and customers early. Set up contingency plans, like alternate routes or backup carriers, for disruptions. For instance, if a winter storm hits, reroute to a warmer port or switch to rail.
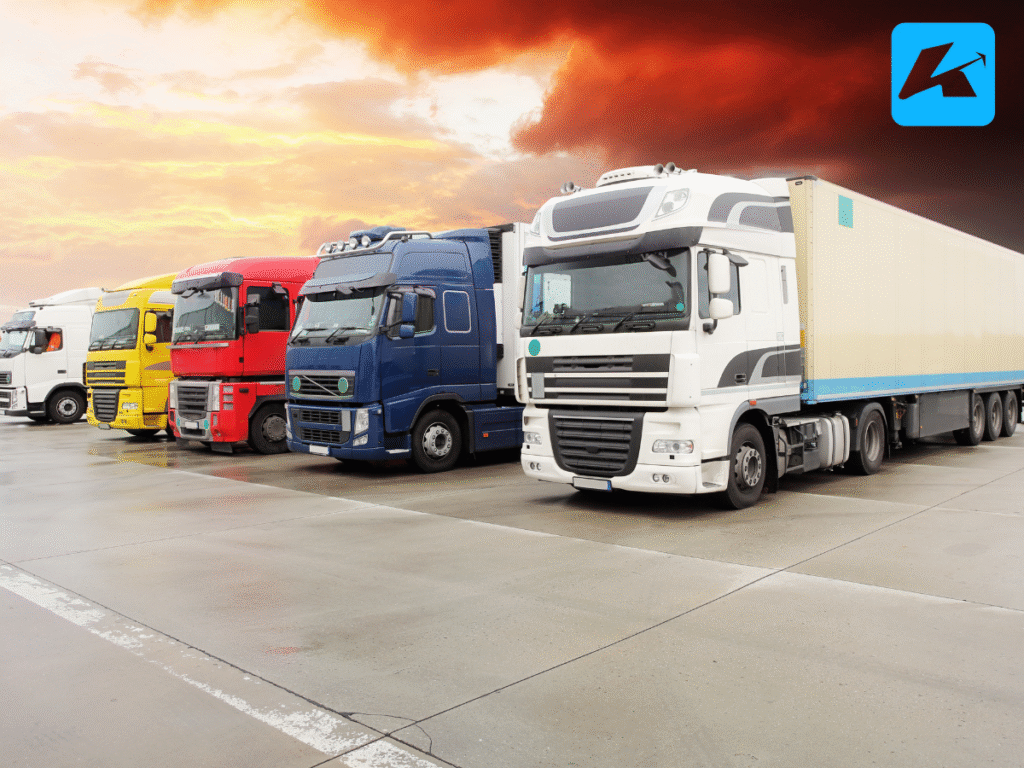
Regular check-ins with partners ensure everyone’s aligned and ready to pivot.
How to Start: Create a peak season communication plan. Schedule weekly calls with carriers and suppliers to review progress and address risks.
Putting It All Together
Peak business seasons test your logistics, but with the right strategies, you can turn challenges into wins. By planning early, optimizing inventory, partnering wisely, leveraging tech, and staying flexible, you’ll keep your supply chain running smoothly.
These steps aren’t just about surviving the rush—they’re about delivering on time and keeping customers happy. At Kargage, we’ve seen proactive shippers shine during peak seasons with our support. But this isn’t about us—it’s about you.
Ready to streamline your next peak season? Call us at (727) 628-3545 for a quote. With this guide, you’re set to conquer the busiest times like a pro.